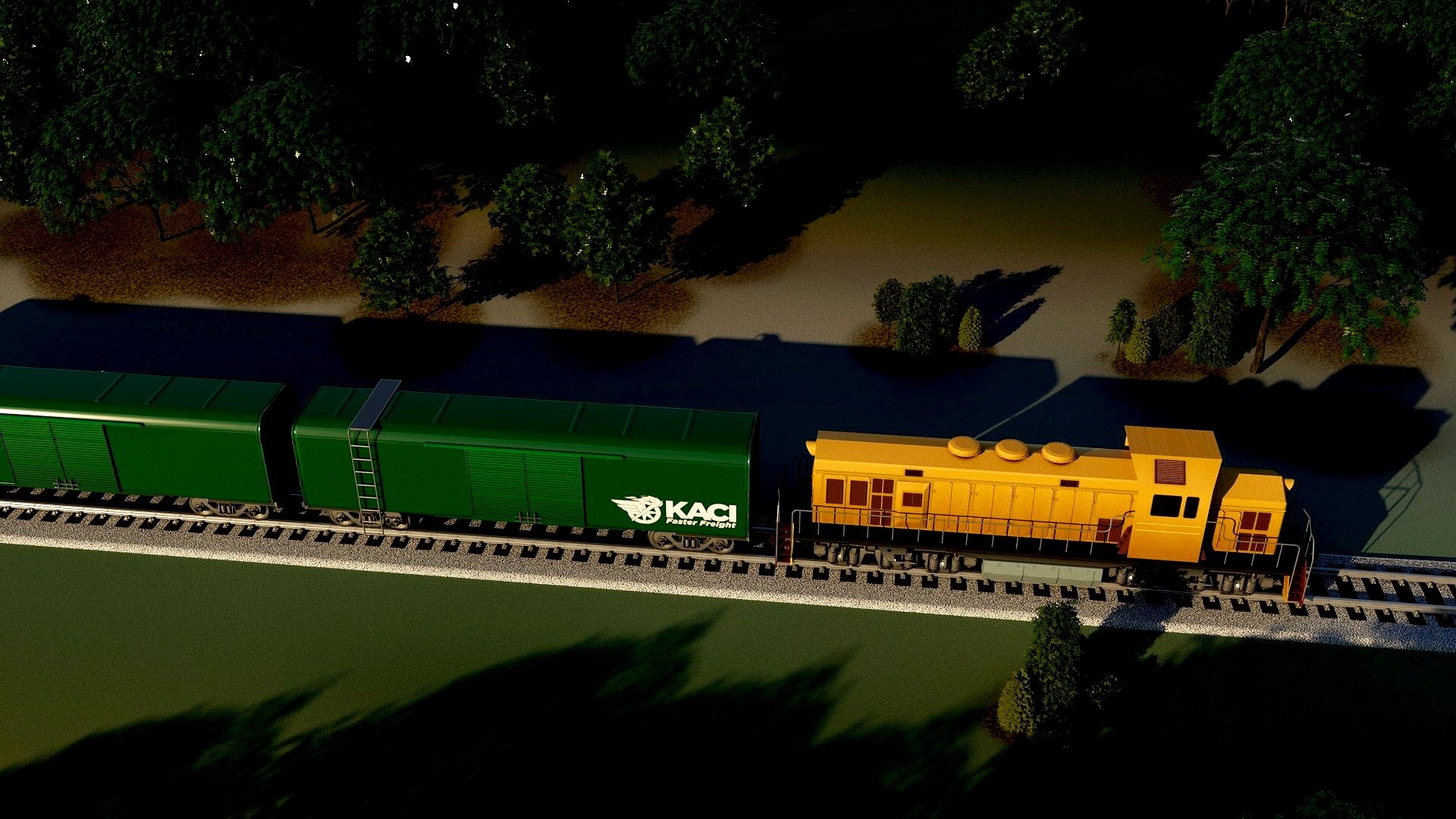
Modern logistics design with patent pending status in North America and Australia.
Next-Generation Rail Service
Our process combines the efficiency of rail with the flexibility of trucking.
This is possible because KACI terminals move railcars side-to-side, allowing them to break unit trains down into individual cars for precise single wagon handling. Each railcar is positioned at a dock for end-loading, just like a truck.
This innovation brings trucking-like service quality to rail, enabling pallet-level shippers to shift their freight from trucks to trains.
Leverages Existing Technology
A high-capacity boxcar with end-loading doors holds the payload of 4 full-sized trucks
A lateral-moving traverser breaks down a train’s linear structure, positioning individual rail cars on a dock, just like a truck.
KACI Truck/Train Transload Terminal
Truck-Like Flexibility Shifts Freight from Road to Rail
KACI redefines rail to meet modern demand, enabling rail to handle smaller, more frequent shipments—a capability currently limited to trucking.
The trucking market is valued at over $750 billion, while containerized intermodal freight remains underutilized at $40-60 billion highlighting a powerful growth opportunity.*
Opening rail to shipments of all sizes will drive a monumental shift of freight from road to rail, driving down costs, reducing congestion, and paving the way for modern, scalable logistics solutions.
*Global Market Insights. (2024). Intermodal Freight Transportation Market Size, Forecasts Report 2032; currency in US Dollars
Direct Rail Access
Streamlines Logistics: Direct rail access to factories and distribution centers eliminates costly truck connections.
Enhances Inventory Control: Faster delivery via direct rail access improves inventory management, supporting just-in-time systems.
Real-Time Control: Optimizes delivery and network flow, bringing faster turnarounds and better asset utilization.
Switching Simplified
Dynamic Control: Single wagon handling shuffles railcars in and out of sequence, dynamically. This speeds unit train breakdown and reassembly.
Cost Reduction: KACI’s train consist building method saves time reduces land and labor requirements.
Single Wagon Transport: Enhances network utilization, and enables a hub-and-spoke rail network.
Scalable
KACI’s smaller footprint reduces costs and enables smaller terminals closer to areas of demand.
Custom Solutions
KACI enables flexibility from transloading, to specialized intermodal like RORO, refrigerated freight or automobiles.
KACI Terminal Cost Data
Proven Cost Advantages
KACI’s smaller physical footprint cuts CapEx by up to 65%when compared to traditional double stack intermodal through lower construction costs and real estate requirements.**
More Freight for Lower Cost
KACI terminals cut OpEx by up to 10% due to reduced labor costs when compared to double stack.**
KACI Boxcars move 30% more volume and 40% more tonnage vs double stack.**
Double-Stack versus Boxcar – Volume Comparison
** WSP. KACI Terminal Conceptual Cost Study - Australia. Prepared for KACI, 2023